Join us at the European Coatings Show 2025 in Nuremberg, Germany from March 25-27, 2025.
Arkema is glad to unveil for this new edition the most recent innovations to meet expectations for a more sustainable life-style, and to further decarbonization and more circularity across the industry !
The Group will leverage its pioneering specialty resins and additives offering, and expertise in the lowest Volatile Organic Compound technologies, to build solutions-oriented answers addressing sustainability, high performance, and anticipation on regulatory evolutions.
Make your coatings, inks and adhesives more sustainable!
Our solutions
Home & Living comfort
High-performance and bio-based products for paints and wood coatings, with up to 93% bio-based content, reduced TiO2 usage, and innovative recycled-based powder coatings for metal furniture with up to 40% recycled content, all while enhancing durability of furniture and flooring with up to 100% bio-based materials, enabling more circular housing applications.
Building efficiency
Enhance indoor and thermal comfort, reduce air conditioning consumption with cool roof coatings, protect and waterproof construction coatings, ensure easy-to-clean and UV-resistant roofing and facades, and provide high thermal and chemical performance to sealants and adhesives.
Resilient infrastructure
We contribute to decarbonizing the built environment by using more safer materials with lower embodied carbon and long-lasting performance, including 2K waterborne NISO systems, high-yield and UV/EB coil coatings, superdurable and hyperdurable coatings, durable and fast-cure protective industrial coatings, and intumescent coatings for fire protection.
Mobility
Mobility is driving new needs and fostering innovation within the automotive sector. This includes advancements in sound dampening solutions to reduce noise, EV battery insulation coatings for safety, corrosion and impact protection for battery casings, new vehicle refinish and OEM coatings for durability and chemicals to assemble electronic components and maintain their integrity.
Conferences & Product Push
Abrasion resistance improvement : High-Performance additives for a sustainable world
Arkema, as a key raw material supplier, participates in your formulation development. This presentation will focus on its high-performance additives, particularly for improving abrasion resistance in coating.
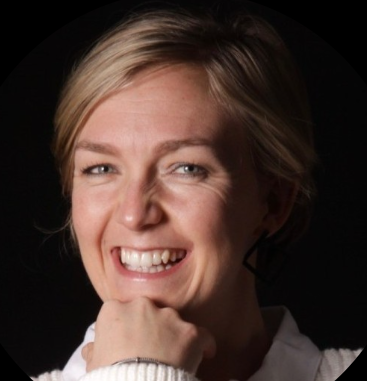
Thought Leaders panel - Carbon footprint reduction across coating value chain
- Driving the changes: Addressing consumer expectations and the request for more informed choices,
- Inventing the paint of the future: Introducing low-carbon options with bio-circular content, leveraging formulation intelligence,
- Decarbonizing the built environment: A Roadmap to Net-Zero Prepainted Metal Infrastructure
- Transforming the EV market: Exploring how coatings play a role in improving EV battery safety and enabling lower carbon intensive processes.
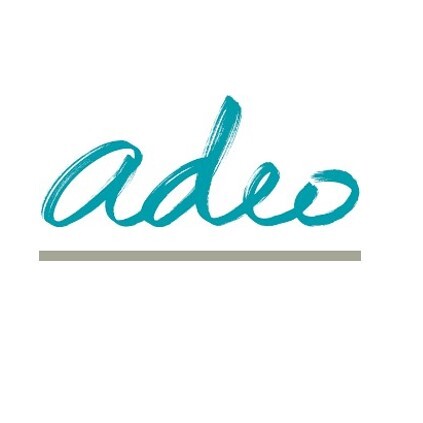
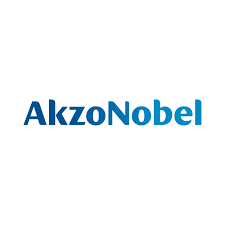
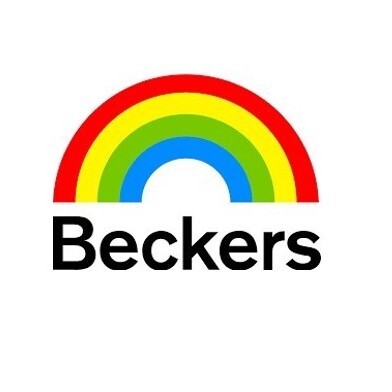
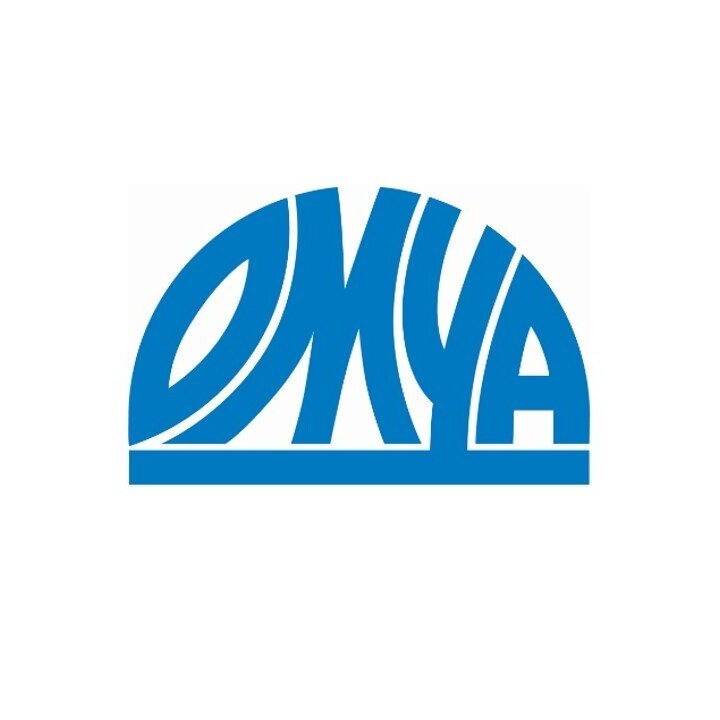

On the way to lower carbon emissions of the coil coating industry
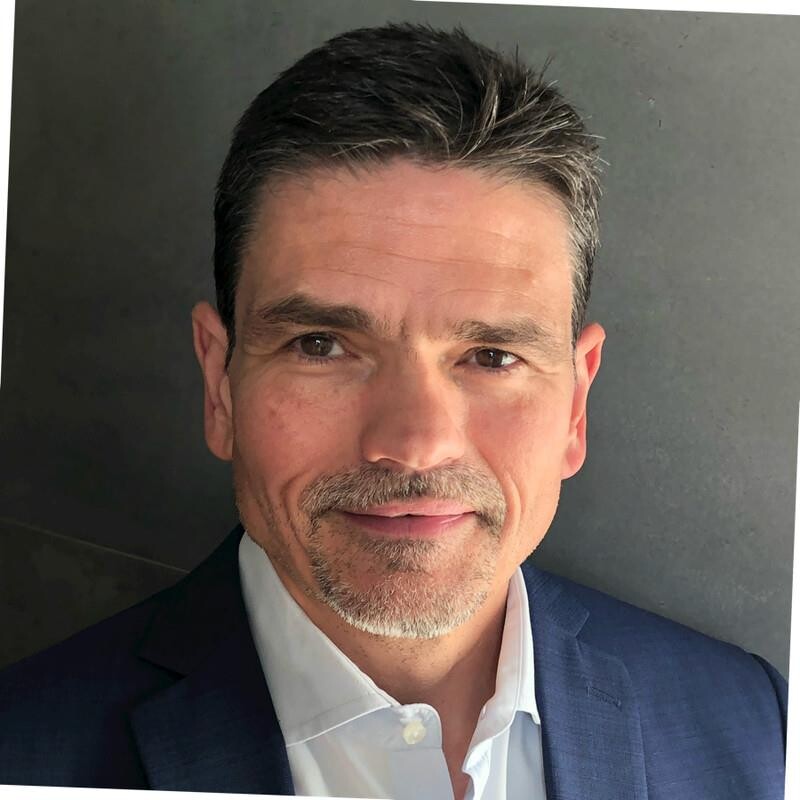
Improving the water resistance of waterborne alkyd emulsion binders
Among the various requirements such as UV resistance, hardness, and dirt pick-up resistance, achieving water resistance remains one of the most challenging. Exterior substrates are exposed to severe weather conditions throughout their lifespan, leading to issues like whitening, blistering, and surfactant leaching.
Relying on the polymerizable surfactant technology, a new generation of alkyd emulsions has been developed and exhibits excellent water resistance. The relationship between alkyd emulsion composition, polymerizable surfactant and their water resistance has been studied to optimize the paint formulation.
Other coating applicative performances are studied. Examples of formulation optimization will be presented and discussed.
A unique collaboration between three industry-leading companies, mapping formulation space, leading to carbon footprint reduction and optimised performance
The paints and coatings industry is working on the decarbonization of the value chain. Multiple routes are being followed according to the product and industry involved. To solve the issues associated with this transition, collaboration is essential. To this end, we have created a three-way collaboration between two raw material suppliers and a paints manufacturer to demonstrate the potential.
The goal of this study was to see to what extent existing formulation practices can be enhanced and stretched, to significantly reduce the carbon footprint of a decorative wall paint. Specifically, by using designed experiments and high-throughput-experimentation, it has been possible to create a performance map showing the extent and possibilities of carbon reduction. Raw materials based on renewable resources, recycled content and /or a mass-balance approach have been investigated. We used the latest data on carbon footprint, to understand what can be achieved if a reduction of 50% is targeted. Indeed, thanks to high-throughput experiments, a balance of performance versus the carbon reduction can be anticipated even beyond 50%.
Advances in high-performance 1-K PVDF/acrylic Hybrid Dispersion for protective coating applications
Viscoelastic behaviour of powder coatings cured at low temperature
In this study, rheological measurements have been utilised to determine the different phases taking place during the film formation process of powder coatings cured at low temperature. The use of dynamic viscosity/time (temperature) cure curves is a powerful technique to quantify formulation and resin parameters. The final aim is to identify the effect of certain resin features on the curing process to enhance resin design.
A variety of powder coatings were used in this study to cover the core market offer: HAA and TGIC polyester and hybrid epoxy-polyester systems.
Transforming coatings innovation through Ecodesign
Practical information
- When?
From March 25 to 27, 2025
- Where?
Messezentrum
90471 Nuremberg
GERMANY- Booth?
Hall 3A Booth #308